Non-destructive testing (NDT) of composite materials has become a critical part of quality assurance in industries such as aerospace, automotive, energy, and marine. A question we frequently receive is whether Technology Design (TD) equipment can be used for ultrasonic inspection of composites. The answer is an unequivocal yes, and here’s why.
The Role of Ultrasound in Composite Inspection
Ultrasonic testing (UT) is a well-established technique for inspecting composite materials. Unlike traditional metals, composites such as carbon fibre-reinforced polymers (CFRP) and glass fibre-reinforced polymers (GFRP) present unique inspection challenges due to their anisotropic and layered structures. UT methods, particularly pulse-echo and phased array ultrasonic testing (PAUT), are highly effective in identifying common flaws such as:
- Delamination’s
- Dis bonds
- Voids
- Fiber waviness
- Inclusions
Ultrasound is especially useful because it can penetrate thick and multilayered components while offering high-resolution imaging and accurate depth information.
Key Considerations for Composite UT
Choosing the right UT solution for composite inspection depends on several key factors:
- Material type and fiber orientation: Affects wave propagation and attenuation.
- Thickness of the component: Thicker sections may require lower-frequency probes for deeper penetration.
- Surface topography: Curved or complex geometries may necessitate flexible wedges, immersion setups, or encoded scanning systems.
- Required resolution: Dictates the use of high-frequency probes and digital signal processing.
- Inspection method: Manual or automated, depending on throughput, access, and repeatability requirements.
Features That Matter
Modern UT systems are expected to be intuitive, configurable, and highly capable. At TD, we recognize these needs and offer equipment that includes:
- Dedicated pulse-echo and phased array electronics
- Manual and automated scanning solutions
- Wide bandwidth and dynamic range for diverse material applications
- Advanced gate functionality (hardware and software)
- Comprehensive calibration tools including TCG and DAC
- User-friendly interfaces for quick setup and analysis
These features enable users to comply with rigorous inspection standards such as ASTM E2580 (ultrasound of composites) and NADCAP requirements, while also improving inspection efficiency and traceability.
Serving Demanding Industries
TD systems are deployed globally in sectors where failure is not an option:
- Aerospace and defense: Inspecting aircraft fuselages, wings, and rotor blades
- Space exploration: Ensuring structural integrity of lightweight yet high-performance materials
- Wind energy: Evaluating turbine blades for subsurface flaws
- Automotive and transportation: Checking high-performance parts for flaws that affect strength and weight
Whether it’s for R&D, production-line inspection, or field-based maintenance, TD’s FocusScan RX II, PS45 PocketScan, and TD Scan software can simplify your composite inspections and deliver precise, reliable results.
Learn more about our acquisition solutions for ultrasonic NDT inspection of composites.
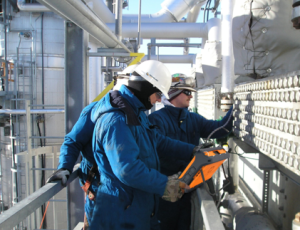
Advanced Phased Array